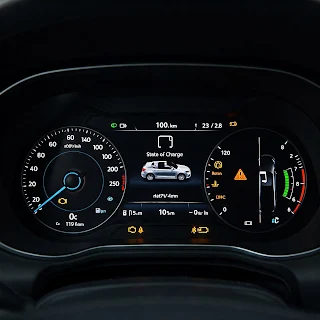 |
SOC Jump in EV Vehicle Cluster |
- Battery Management System (BMS) Recalibration:
The BMS is the
"brain" of your EV's battery. It constantly monitors various
parameters like voltage, current, temperature, and the state of individual
cells within the battery pack. One of its crucial functions is to estimate and
display the State of Charge (SOC). Over time, minor inaccuracies can creep into
the SOC calculation. To maintain accuracy, the BMS periodically performs a
recalibration.
How?:
During recalibration, the BMS might make adjustments to its internal algorithms
based on the latest readings. This can sometimes result in a sudden jump in the
displayed SOC, especially near the extremes of the charge range (close to 0% or
100%). Think of it like the BMS "double-checking" its calculations
and making a correction.
Is it normal? Yes,
occasional recalibration is a normal and healthy part of battery management. It
ensures the SOC reading remains as accurate as possible.
EV
manufacturers regularly release software updates to improve various aspects of
the vehicle, including the battery management system.
How?: A
software update might change the way the BMS calculates or displays the SOC. It
could also introduce new algorithms for estimating SOC or refine existing ones.
These changes can sometimes lead to a noticeable jump in the SOC display.
Is it normal? Generally,
yes. Software updates are designed to improve performance and accuracy. A
change in SOC display after an update isn't usually a cause for concern, as
long as the overall battery performance remains normal.
If you
consistently charge your EV to a certain level (e.g., 80%) and then suddenly
decide to charge it to 100%, the BMS needs to adjust to this change.
How?: The
BMS learns your charging habits. If you always stop at 80%, it might have
optimized its SOC estimation for that range. When you charge to 100% for the
first time in a while, the BMS might need to recalibrate its understanding of
the full battery capacity, leading to a jump in the SOC display.
Is it normal? Yes, this is
a normal response to a change in charging habits. It's the BMS adapting to the
new charging pattern.
Battery
performance is affected by temperature. Extreme heat or cold can impact the
battery's chemical reactions and its ability to hold a charge.
How?: The
BMS takes temperature into account when calculating SOC. If the temperature
changes significantly (e.g., you park your car in the sun on a hot day), the
BMS might adjust the SOC reading to reflect the temperature's impact on the
battery. This adjustment can sometimes appear as a sudden jump.
Is it normal? Fluctuations
in SOC due to temperature are possible, but they are usually gradual. A very
sudden jump due to temperature alone is less likely.
An EV battery
pack consists of many individual cells. For optimal performance and longevity,
these cells need to be balanced, meaning they should have roughly the same
charge level. The BMS performs this balancing act.
How?:
During the balancing process, the BMS might redistribute charge among the
cells. This can sometimes cause small fluctuations in the overall SOC, which
might be perceived as a jump.
Is it normal? Yes, battery
balancing is a necessary process. Minor SOC fluctuations during balancing are
usually not a problem.
Summary:
A sudden jump in SOC isn't always a
reason to panic. It can often be attributed to normal BMS operations like
recalibration, software updates, changes in charging habits, or temperature
variations.
However, it's always a good idea to monitor the situation. If the
jumps are frequent, large, or accompanied by other issues like reduced range,
charging problems, or error messages, then it's best to consult with your EV's
service centre. They can diagnose the issue and ensure your battery is healthy.